Fire sprinkler systems protect lives and property by controlling or extinguishing fires in various structures, including residential, commercial, and industrial buildings. Understanding how these systems work and adhering to local building codes are vital for ensuring optimal fire protection.
This guide will help you navigate the different types of fire sprinkler systems, relevant Minnesota building code requirements, and NFPA 25 standards for inspecting and maintaining these systems.
Fire Sprinkler Systems Explained
Sprinkler systems include a network of piping filled with pressurized water. Even at high pressure, sprinklers do not cause more damage than the fire itself, nor are they triggered by smoke or set off throughout an entire building at once.
Automatic fire sprinklers are activated by heat, not smoke. Each sprinkler head contains a heat-sensitive element, typically a glass bulb filled with glycerin-based liquid.
When the air around the bulb reaches a specific temperature, usually between 135-165 degrees Fahrenheit, the liquid expands, shattering the bulb. This activates the sprinkler head, letting pressurized water from the piping system flow out. Note that only the sprinkler head or sprinkler heads nearest to the fire will activate.
There are four main types of residential and commercial fire sprinkler systems. Each design adapts to the needs of various facilities to ensure proper protection. Let’s explore these four fire sprinkler systems and their primary applications.
Different Types of Sprinkler Systems
Wet Pipe Sprinkler System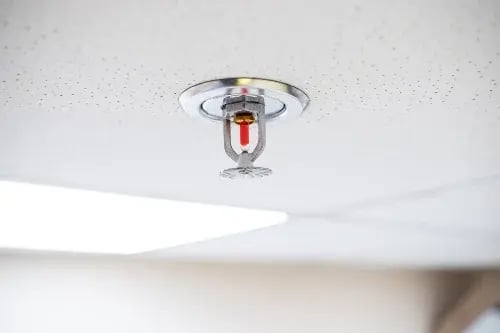
Wet pipe sprinkler systems are the most common type, using sprinkler heads connected to pipes filled with pressurized water. When heat from a fire is detected, the sprinkler heads discharge water to contain or extinguish the fire. However, these systems would not work in freezing cold environments, or in areas with water-sensitive equipment.
Dry Pipe Sprinkler System
Dry pipe sprinkler systems use pressurized air or nitrogen in the pipes. A valve prevents water from entering the pipes until the system is activated by a fire, at which point the pressure drops, the valve opens, and water flows through to extinguish the fire. While dry pipe systems require more maintenance and have higher installation costs, they are ideal for areas where freezing is a risk or where water leaks could damage sensitive equipment.
Pre-Action Sprinkler System
Pre-action sprinkler systems, similar to dry pipe systems, contain pressurized air or nitrogen in the pipes. They use an electronic valve that requires both heat and smoke detection to release water. This dual-action mechanism provides an added layer of protection, making pre-action systems suitable for areas where accidental water discharge could cause significant damage.
Foam Water Sprinkler System
Foam water sprinkler systems combine water with a foam concentrate for large-scale fire suppression. These systems can be wet pipe, dry pipe, or pre-action in design, and include a bladder tank for foam. When activated, the foam mixes with water to suppress and smother fires, making them effective for protecting high-value assets (like aircraft, yachts, or motorized equipment).
Understanding the various types of sprinkler systems helps when selecting the right fire protection solution for different environments. However, you also need l to comply with local building codes and regulations to ensure optimal safety and functionality.
Building Code Requirements
The Minnesota Building Code establishes specific protection requirements for fire sprinkler systems across various building types, including commercial, industrial, and residential properties. These regulations align with NFPA 13, which sets the criteria for the design and installation of fire sprinkler systems.
Key Requirements for Different Building Types
Automatic sprinkler systems must be installed according to these specific requirements:
- Commercial and Industrial Buildings
- Building Size and Occupancy: The code specifies requirements based on the building's square footage and occupant load:
- Assembly Occupancies: Buildings such as theaters, auditoriums, and places of worship typically require sprinklers if they exceed 12,000 square feet or have an occupant load of more than 300 people.
- Business Occupancies: Office buildings and other business occupancies often require sprinklers if they are over 12,000 square feet.
- Industrial Occupancies: Factories and industrial facilities must have sprinkler systems if they exceed 12,000 square feet or store hazardous materials.
- Special Hazard Occupancies: Facilities involved in manufacturing, processing, or storing flammable liquids, gases, or chemicals are subject to more stringent sprinkler requirements due to higher fire risks.
- High-Rise Buildings: High-rise commercial buildings, typically defined as structures over 75 feet in height, must have automatic sprinkler systems throughout the entire building.
- Mixed-Use Buildings: In buildings combining retail, office, and residential spaces, the most stringent fire sprinkler requirements for any part of the building apply to the entire structure.
2. Residential Buildings
- Townhouses: An automatic sprinkler system is required in townhouses with three or more dwelling units. Each single-family dwelling unit is considered a separate building and must be equipped with an appropriate fire sprinkler system. Attached garages require one dry head sprinkler, and combustible attached structures (such as patios and decks) must have at least one dry head sprinkler for every 20 linear feet of common wall.
- Multiunit Resort Buildings: Defined as structures with sleeping accommodations on property near recreational spaces like lakes or ski areas, these buildings must have automatic sprinkler systems if they exceed 9,250 square feet.
- Other Residential Buildings: Bed and breakfasts with six or more guest rooms, transient and non-transient boarding houses with more than 10 occupants, and hotels and motels must also adhere to sprinkler requirements.
- High-Rise Residential Buildings: Sprinklers have been required for decades, but older public housing complexes must be retrofitted with current systems by 2033.
- Care Facilities: Dwellings classified as care facilities, such as child and adult day care centers, supervised living facilities, residential hospice facilities, foster care homes, senior housing, nursing homes, and assisted living facilities, must have automatic fire sprinkler systems if they exceed 4,500 square feet.
These regulations provide a safer environment for occupants while reducing the risk of significant fire damage. With sprinkler types and code restrictions covered, let’s talk about how this relates to NFPA 25.
NFPA 25 Installation and Maintenance
As a building or facility owner, you should establish a proactive program for periodic testing, inspection, and maintenance of your fire sprinkler systems–regardless of your system type. Skipping regular maintenance can lead to inoperative fire pumps and sprinkler control valves, which may result in disastrous consequences.
According to the National Fire Protection Association, both wet and dry systems must be tested every five years, with a full performance test for dry systems required every three years. The NFPA 25 Standard for the Inspection, Testing, and Maintenance of Water-Based Fire Protection Systems outlines specific weekly, monthly, quarterly, and annual inspection requirements:
Weekly Inspections
- Fire Protection Mains and Branch Lines: Inspect these components, especially those prone to freezing temperatures, to ensure proper functioning.
- Fire Doors: Visually inspect all fire doors to ensure they are free from obstructions and in good operating condition.
- Fire Alarm Systems: Inspect and test both automatic and manual fire alarm systems.
- Gauges: Visually inspect gauges on dry, pre-action, and deluge systems to verify normal water and air pressures.
Monthly Inspections
In addition to the weekly inspections, perform the following monthly tasks:
- Control Valves: Ensure all control valves are accessible, free from external leaks, and in their normal positions.
- Gauges on Wet Pipe Systems: Verify normal water pressure and ensure the gauges are in good working order.
Quarterly Tests and Inspections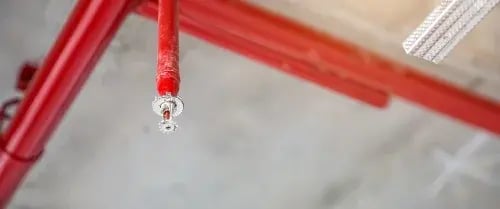
- Hydraulic Sprinkler Systems: Ensure the nameplate is legible and securely attached to the riser.
- Water Flow Alarm Devices: Test and inspect these devices to ensure they are in good working condition.
- Pressure-Reducing Valves: Inspect these valves to ensure they are open, free from leaks, and in good condition.
- Mechanical Water Flow Alarm Devices: Test these devices quarterly. Semi-annual inspections are acceptable for vane-type or pressure switch-type alarm devices.
- Fire Department Connections: Inspect these connections to ensure they are in place, visible, accessible, free of physical damage, and functioning properly.
Annual Tests and Inspections
Due to their complexity, annual fire sprinkler inspections should only be performed by licensed sprinkler contractors. The NFPA 25 provides detailed instructions for these procedures, which include:
- Sprinklers, Hangers, Pipes, and Fittings: Test these components to ensure they are in good working condition.
- Main Drain Tests: Conduct tests on all sprinkler systems to verify control valves are open and functioning properly.
- Dry Pipe Valves: Clean, reset, and perform a throttle trip test.
- Deluge Valves: Conduct a full trip test at least once a year if possible. Avoid waiting longer than three years between tests.
- Antifreeze Solution: Test and adjust the antifreeze solution in the systems if necessary.
- Nozzles on Water Spray Systems: Visually inspect and test these nozzles for proper flow.
- System Strainer: Remove and visually inspect the system strainer for damage, replacing any corroded parts.
Preventing Loss with Testing and Inspection of Fire Sprinkler Systems
Any sprinkler that shows signs of leakage, corrosion, physical damage, or loss of fluid must be replaced. Regular testing and inspection ensure your building remains protected in the event of a fire. Partnering with a fire monitoring service ensures your fire sprinkler systems are routinely inspected and tested, guaranteeing their proper functionality at all times.
Understanding and maintaining fire sprinkler systems can help protect lives and property from fire damage. By knowing the different types of systems and adhering to Minnesota building codes, you can ensure optimal safety.
Regular inspections and maintenance, as detailed by NFPA 25, help keep your systems in top condition. If you need assistance with keeping your fire sprinkler system thoroughly monitored and maintained, reach out to Brothers Fire & Security for a personalized quote. Our experts are here to help you safeguard your property and ensure your fire protection systems are always ready when you need them.
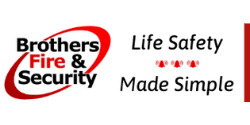
For Immediate Assistance Call
800-607-2767
.png?width=225&height=225&name=unnamed%20(1).png)
Stephen Cieslukowski, President,
Brothers FIre & Security
- Online Safety Courses
- Fire Protection Systems
- Fire Alarm Systems
- Suppression Systems
- Inspections & Service
- Fire Sprinkler Systems
- Fire Extinguishers
- Kitchen Hood Systems
- Security Systems
- Access Control Systems
Privacy Policy: We promise to keep your email address safe